In-depth Introduction: What is Internal Grinding?
Essential for modern manufacturing, internal grinding meets the demand for high precision and quality finishes.
Internal grinding is a key process for achieving precise finishes on internal hole surfaces, vital in industries like automotive, aerospace, and toolmaking. It works on various materials and hole shapes, offering excellent surface quality and tight tolerances.
This article covers the basics, methods, and applications of internal grinding across industries.
What is Internal Grinding?
Internal grinding is a specialized machining process aimed at refining the inner surfaces of workpieces, typically through the use of a rotating grinding wheel. This technique is particularly effective for processing features such as through holes, blind holes, and stepped holes. What sets internal grinding apart from other machining techniques is its ability to achieve tight tolerances and fine finishes on the internal surfaces of a workpiece.
One of the key advantages of internal cylindrical grinding is its ability to process hardened materials. This makes it a highly sought-after process in industries like aerospace, automotive, and medical device manufacturing, where precision is paramount. It provides consistent and high-quality results, ensuring that parts meet strict design specifications and performance standards.
Types of Grinding and Their Comparisons
Grinding is a fundamental technique used for smoothing and shaping workpieces. Depending on the surface being worked on, the grinding method can vary. Here’s a breakdown of different grinding types and how they compare:
External Cylindrical Grinding: This method is used to grind the outer surface of workpieces, such as shafts and rods. The workpiece rotates while the grinding wheel moves along its axis. It is a straightforward process with a simpler machine structure.
Internal Cylindrical Grinding: Internal grinding, in contrast, works on the inner surfaces of a workpiece, such as holes and cylindrical cavities. It requires a more complex machine setup, including specialized grinding heads and support mechanisms.
Surface Grinding: This technique is used to grind flat surfaces, such as planes or steps. A flat grinding wheel moves linearly across the workpiece, providing a smooth finish. It is typically employed for parts that don’t require cylindrical or internal features.
Centerless Grinding: Unlike external cylindrical grinding, centerless grinding doesn’t require a center hole for positioning. Instead, the workpiece is held in place using the pressure from a grinding wheel and a regulating wheel. This method is well-suited for high-volume production and parts that require fine surface finishes.
Each grinding method has its unique applications and is chosen based on the nature of the workpiece and the desired outcome. Understanding these distinctions can help manufacturers make the best choice for their machining needs.
Internal Cylindrical Grinding vs. External Cylindrical Grinding
While both internal and external cylindrical grinding are used for precision machining, there are significant differences between the two methods:
Wheel Size and Speed: Internal cylindrical grinding uses smaller wheels and operates at lower speeds (typically 20–30 m/s). This slower speed can result in a slightly rougher surface finish compared to external grinding, which uses larger wheels at higher speeds for a smoother result.
Contact Area: Internal grinding involves the grinding wheel contacting the inner surface of a workpiece in an inscribed circle. This results in a larger contact arc, increasing grinding forces and generating more heat. This heat can lead to issues such as wheel wear and workpiece overheating, which must be carefully managed.
Chip and Coolant Management: In internal grinding, the confined space within the workpiece makes it harder for coolant to reach the grinding zone and for chips to be expelled. This can lead to wheel clogging and negatively impact the quality of the surface finish.
Rigidity and Vibration: The extended shaft used in internal cylindrical grinding is less rigid, which can cause vibrations and lead to inaccuracies in the machining process. This limits the grinding feed rate and can impact both surface quality and dimensional accuracy.
These differences highlight why internal grinding is a more challenging process and requires specialized equipment to achieve optimal results.
Methods of Internal Cylindrical Grinding
Internal cylindrical grinding typically involves two main methods: longitudinal grinding and plunge-cut grinding.
Longitudinal Grinding: This method involves the grinding wheel moving along the length of the workpiece. It is essential to maintain proper cooling and chip removal to prevent heat buildup and ensure the accuracy of the grinding process. This method is commonly used for stepped holes, requiring precise adjustments to maintain coaxiality.
Plunge-Cut Grinding: The plunge-cut method is more efficient for shorter internal lengths, as it reduces machining time. This method requires a rigid grinding shaft to maintain accuracy. However, because it generates higher forces, the grinding wheel tends to clog more quickly and needs frequent dressing to maintain its effectiveness.
Both methods have their advantages, and the choice between them often depends on the specific requirements of the workpiece and the desired machining efficiency.
Choosing Internal Grinding Wheels
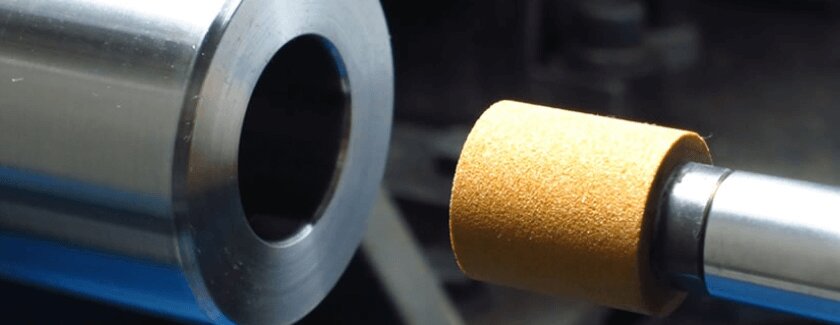
Selecting the right grinding wheel is critical for achieving high-quality results in internal grinding. The following factors should be considered:
Wheel Diameter: The diameter of the grinding wheel should be appropriately matched to the hole diameter. A typical ratio is between 0.5 and 0.9. For larger hole diameters, a smaller ratio should be used, while smaller diameters benefit from a larger ratio.
Wheel Width: A wider wheel improves surface finish and efficiency but can also increase grinding forces, potentially leading to shaft deformation. The width of the wheel should be balanced to ensure optimal performance without excessive wear or deformation.
Wheel Hardness:
Softer Wheels: Suitable for high-hardness materials, as they maintain sharp grains that reduce heat buildup and improve cutting performance.
Harder Wheels: Best for low-hardness materials, as they ensure long-lasting abrasiveness and prevent rapid grain shedding.
Wheel Grit Size: Coarser grit sizes (e.g., F36, F46) enhance cutting force and are useful for high-speed grinding without causing burns. Fine grit sizes are generally used for achieving smoother finishes.
Wheel Shape: Internal grinding typically uses flat or single-sided recessed wheels. Single-sided recessed wheels are ideal for grinding both the internal surface and end faces of stepped holes.
Choosing the right grinding wheel for the task is essential for ensuring efficient and high-quality internal grinding.
Internal Grinding: Workpieces and Applications
Workpiece Types
Internal cylindrical grinding is primarily used to work on the inner diameters of various components. Common workpieces include shafts, sleeves, bearings, gears, and cylinders. This process allows manufacturers to achieve highly precise inner dimensions, ensuring that parts fit together perfectly in assemblies.
Application Fields
Automotive Industry: Internal grinding is crucial for producing high-precision components like crankshafts, camshafts, and connecting rods that require tight inner diameter tolerances.
Machinery Industry: These machines are used to manufacture mechanical components, particularly those involving shafts and gears, which need to be precisely machined for optimal performance.
Aerospace Industry: Internal cylindrical grinding plays a vital role in creating high-precision aerospace components, including engine parts and bearings, where dimensional accuracy is critical.
Electronics Industry: This technique is also applied in the electronics sector for manufacturing precise parts such as magnetic heads and semiconductor devices.
Conclusion
Internal cylindrical grinding is an indispensable technique in modern manufacturing, offering the precision and flexibility needed to meet the demanding specifications of various industries. While it presents challenges like chip removal and the potential for overheating, its ability to produce high-quality internal surfaces makes it a critical process for many applications. By selecting the right grinding method and wheel, manufacturers can optimize their processes and achieve superior results.