Grinding Burn – What Can I Do?
In high-precision manufacturing, surface quality is critical. Whether in aerospace, automotive, or mold industries, grinding burn—though seemingly minor—can lead to part rejection, delivery delays, and loss of customer trust. Worse still, it often goes unnoticed in the early stages.
When grinding burn occurs, you can start by examining heat sources, evaluating coolant effectiveness, checking wheel condition, and reviewing process parameters. Combined with proper detection methods, this helps determine the extent of the issue. On a deeper level, improving the thermal stability and process control of the grinding machine itself can significantly reduce burn risk.
If you're facing surface discoloration, hardness anomalies, or part failures, this article offers practical insights to help you improve your grinding process.
1. What Causes Grinding Burns?
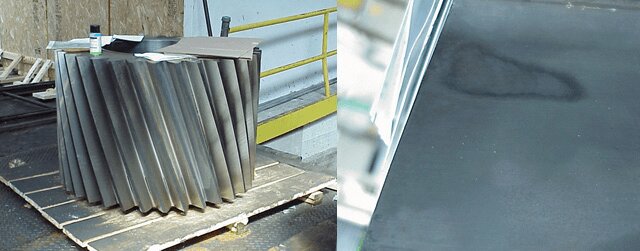
Grinding burn occurs when excessive heat generated during the grinding process alters the surface or subsurface of a material. This thermal damage can result in discoloration, reduced hardness, micro-cracks, and in extreme cases, residual tensile stresses that can compromise the structural integrity of the part.
The main causes of grinding burn include:
˙Excessive grinding heat due to high material removal rates, dull wheels, or excessive friction.
˙Inadequate cooling, which prevents sufficient heat dissipation in the grinding zone.
˙Improper grinding parameters, such as high feed rates, deep cuts, or excessive wheel speeds.
˙Wheel wear or glazing, which reduces cutting efficiency and increases heat generation.
˙Material sensitivity, especially with heat-treated steels and alloys prone to tempering or re-hardening.
˙Unstable fixturing, which leads to uneven grinding pressure and localized overheating.
It’s also worth noting that the machine itself can be a root cause. Machines with poor thermal stability, vibration issues, or lacking in adaptive control features can significantly increase the risk of burn, even when the grinding parameters appear correct. That’s why process reliability must include the selection of the right grinding machine.
2. Avoidance Starts With Detection
You can’t fix what you can’t detect. Grinding burn is especially dangerous because it may not be visible to the naked eye. Surface color change is one indicator, but not always present or reliable.
There are several ways to identify grinding burns effectively:
Visual Inspection
Surface discoloration (blue, brown, or dark gray areas) may indicate overheating. However, this is only a surface-level clue and often misses subsurface damage.
Nital Etching (Chemical Testing)
This technique uses an acid solution to reveal structural changes in the material. It's especially effective for detecting re-tempering or re-hardening caused by thermal damage.
Microhardness Testing
Localized hardness changes are strong indicators of grinding burn. If the hardness profile shows unexpected softening or hard zones, thermal damage is likely.
Eddy Current or Magnetic Particle Inspection
These non-destructive methods can detect subsurface cracks or changes in material structure caused by grinding burn.
Thermal Monitoring Systems
Modern grinding machines can include real-time temperature sensors that detect abnormal heat levels during the process. These systems are highly effective for preventing burn before it occurs.
3. Tips for Avoiding Grinding Burn
Once you understand the causes and know how to detect grinding burns, the next step is implementing preventative measures. Here are some proven, practical strategies you can apply:
Optimize Grinding Parameters
˙Use lighter passes rather than deep single cuts.
˙Adjust feed rates and wheel speed to reduce heat input while maintaining efficiency.
˙Utilize simulation or process monitoring tools to predict temperature thresholds.
Improve Cooling Performance
˙Use high-performance grinding fluids designed for both lubrication and cooling.
˙Ensure the coolant nozzle is properly positioned and delivers adequate flow and pressure.
˙Avoid coolant starvation, especially in high-speed grinding operations.
Maintain Your Grinding Wheel
˙Dress and true the wheel regularly to prevent glazing and maintain cutting sharpness.
˙Use wheels with appropriate grain, bond, and hardness for the material and grinding type.
˙Ensure the wheel is balanced and running without vibration.
Review Fixture Design and Machine Setup
˙Make sure the part is clamped securely to avoid vibration or uneven pressure.
˙Monitor machine load and vibration to detect any instability during the operation.
˙Where possible, use machines with automatic thermal compensation or feedback systems.
4.How MINNUO Grinding Machines Effectively Prevent Grinding Burn
From structural design to control systems, MINNUO grinding machines are optimized around thermal control to ensure process stability and prevent grinding burn.
Spindle temperature control and thermal compensation: The spindle uses an oil cooling system, combined with thermocouples for real-time temperature monitoring. The system performs automatic thermal displacement compensation to ensure dimensional stability during long-term machining.
Grinding load monitoring: By collecting spindle power and torque data, the system enables real-time monitoring of the grinding status, allowing early detection of wheel dulling, overload, and other abnormalities to prevent localized heat concentration and burn.
High rigidity and low-vibration structure: The one-piece cast iron machine base, combined with vibration-damping design, effectively reduces machining vibration and minimizes heat caused by friction or impact.
High-pressure precision cooling system: Multi-point adjustable nozzles with a high-pressure pump ensure that coolant is delivered directly to the grinding contact zone, rapidly removing heat and eliminating cooling blind spots.
This thermal management-focused system design allows MINNUO machines to maintain excellent thermal stability in long-cycle, high-precision grinding, significantly reducing the risk of burn.
Conclusion: Turn Problems into Opportunities, and Equipment into Solutions
Grinding burn is more than a quality issue—it reflects the stability of thermal control in your process. Mastering detection, optimizing parameters, and upgrading equipment are key to improving machining reliability.High-performance grinding machines with temperature monitoring, process feedback, and intelligent adjustment provide stronger protection for your production.MINNUO offers not just machines, but forward-looking grinding solutions.
If you're optimizing your process or evaluating new equipment, contact the MINNUO technical team for expert advice and solutions tailored to your needs.