What are the Differences Between Vertical and Horizontal Lathes?
In the current global political and economic landscape, the importance of manufacturing is increasingly prominent, making it a key area for international competition. U.S. President Donald Trump’s attempts to drive manufacturing back to the U.S. by imposing high tariffs on foreign-made products highlight the strategic importance of the manufacturing sector for a country’s economy, employment, and national security.
As core processing equipment, the selection of lathes directly impacts an enterprise’s production efficiency, product quality, and cost control. Vertical lathes, with vertical spindles, are ideal for processing large, disk-shaped, and ring-shaped parts, where gravity aids in stabilizing the workpiece. Horizontal lathes, with horizontal spindles, are more suitable for processing shaft-type and sleeve-type parts, with easier axial feeding. Choosing the right lathe can boost a company’s competitiveness, whereas the wrong choice may put them at a disadvantage.
Next, let’s dive into the differences between vertical and horizontal lathes to guide your selection.
I. Basic Concepts and Core Differences Between Vertical and Horizontal Lathes
(a) Differences in Spindle Orientation and Structural Design
Comparison Item | Vertical Lathe | Horizontal Lathe |
Spindle Orientation | Vertical | Horizontal |
Worktable | Large diameter, ideal for clamping large disk-shaped and ring-shaped parts | Relatively smaller, suitable for clamping shaft-type and sleeve-type parts |
Bed Rails | Vertical, supports workpiece gravity | Horizontal, guides tool movement |
Structural display | ![]() | ![]() |
(b) Differences in Machining Characteristics
Comparison Item | Vertical Lathe | Horizontal Lathe |
Suitable Workpieces | Large disk-shaped, ring-shaped parts, such as large flanges, gears, etc. | Shaft-type, sleeve-type parts, such as drive shafts, sleeves, etc. |
Machining Advantages | Convenient clamping, gravity minimizes influence on machining precision | Axial feeding is convenient, excelling in shaft-type machining precision |
Machining Limitations | Limited axial machining length | Challenging for processing large disk-shaped workpieces |
(c) Differences in Precision Performance
In high-precision shaft-type machining, horizontal lathes, with their mature rail systems and stable transmission structures, achieve superior straightness and cylindricity. Vertical lathes, on the other hand, have an advantage in processing the flatness and verticality of large disk-shaped parts, especially for larger diameter workpieces, where gravity distribution is even, minimizing deformation errors due to gravity. However, in terms of controlling axial dimension precision, vertical lathes are relatively weaker.
(d) Differences in Production Efficiency
In small-batch, multi-variety production, horizontal lathes stand out for their flexibility. They can quickly adapt to different workpieces with fast tooling and program changes. However, in large-batch production of large disk-shaped parts, vertical lathes exhibit high efficiency, with large worktables that can clamp multiple workpieces at once, reducing clamping frequency and increasing production efficiency.
II. How to Choose Between Vertical and Horizontal Lathes
(a) Choose Based on Workpiece Type
· Large disk-shaped and ring-shaped parts: Prioritize vertical lathes, such as when processing large flanges with diameters exceeding 1 meter. Vertical lathes can easily clamp these parts and guarantee machining precision.
· Shaft-type and sleeve-type parts: Horizontal lathes are the best choice, for instance, when machining automotive drive shafts. Horizontal lathes excel in providing precise axial feeding, ensuring high machining accuracy.
(b) Choose Based on Precision Requirements
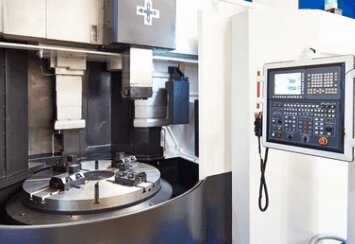
· High-precision shaft-type machining: Choose high-precision horizontal lathes equipped with precision ball screws and high-accuracy bearings to ensure micron-level machining precision.
· Flatness and verticality requirements for large disk-shaped workpieces: Vertical lathes are more advantageous due to their rigid structure and vertically arranged spindles, which effectively ensure machining accuracy.
(c) Choose Based on Production Scale
· Small-batch production: Horizontal lathes are more suited due to their flexibility and cost-effectiveness. They can quickly switch between different workpieces.
· Large-batch production: For large disk-shaped parts, vertical lathes offer high efficiency and stability, which can reduce production costs and increase productivity.
(d) Choose Based on Workshop Conditions and Cost Considerations
· Space Constraints: Vertical lathes save space due to their vertical design, making them ideal for workshops with limited space. However, they often require auxiliary equipment, such as overhead cranes, for workpiece clamping. Workshop layout should take this additional need into account.
· Initial Investment and Maintenance: Vertical lathes have a higher initial investment and are more challenging to maintain. They are suitable for industries with high-precision requirements, such as aerospace and heavy machinery manufacturing. Horizontal lathes, on the other hand, offer better cost performance and simpler maintenance, making them more suitable for small to medium-sized enterprises focused on mass production.
(e) Choose Based on Technical Needs and Automation Level
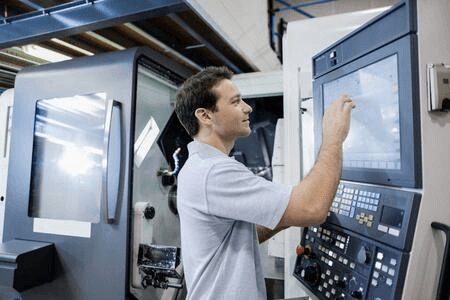
· CNC Systems: Vertical lathes are particularly suited for processing complex curves and high-precision parts, especially with CNC technology. They can efficiently perform complex turning tasks. Horizontal lathes, on the other hand, are excellent in high-speed, repetitive tasks, making them ideal for mass production.
· Additional Functions: Both vertical and horizontal lathes can be equipped with features such as powered turrets and automatic tool changers (ATC). The choice of these functions should depend on the specific production needs. These features can improve machining efficiency, especially in batch production and tasks that require multiple tool changes.
III. Operation and Maintenance Practical Advice
Operating Notes
· Vertical Lathe: Since vertical lathes use vertical clamping, improper clamping can lead to eccentricity and cause vibrations. Operators need to strictly calibrate the clamping accuracy of the workpieces to ensure stability and precision during machining.
· Horizontal Lathe: When machining long workpieces, it is crucial to pay special attention to their support. Insufficient support can lead to deformation or loss of machining accuracy. The use of a tailstock is important when machining long workpieces.
Maintenance and Safety
· Vertical Lathe: Regularly check the rotary table’s lubrication system to ensure smooth lubrication and inspect the spindle bearings for wear. This helps extend the service life of the equipment.
· Horizontal Lathe: Maintenance for horizontal lathes focuses on the upkeep of the rails and checking the precision of the chuck. Also, regular cleaning of debris generated during machining is necessary to prevent chips from accumulating, which could affect performance.
IV. Conclusion: How to Accurately Match Your Needs
Based on different production needs, vertical and horizontal lathes each have distinct advantages. For industries requiring the machining of large, heavy parts such as heavy industry and shipbuilding, vertical lathes are the best choice due to their strong rigidity and stability, making them indispensable for heavy-duty machining tasks. On the other hand, horizontal lathes, with their high cost-performance ratio and excellent production efficiency, are more suited for industries focusing on mass production of small to medium-sized parts, such as automotive components and precision instruments.
If you’re still unsure whether to choose a vertical lathe or a horizontal lathe, feel free to visit our MINNUO website. We offer professional and free consultations to help you find the perfect machining solution tailored to your needs!