What is Multi-axis Machining?
In today’s era of rapid technological advancements, industries like aerospace, automotive, and medical manufacturing are constantly seeking innovative ways to enhance efficiency and precision. Multi-axis machining has emerged as a transformative solution, enabling manufacturers to meet the increasing demand for complex, high-quality parts. With the growing adoption of automation, robotics, and digitalization in smart manufacturing systems, multi-axis machining is not only a hot topic but also an indispensable tool in modern production lines.
So, what is multi-axis machining? It is a cutting-edge machining process where tools or workpieces move simultaneously along four or more axes, often referred to as degrees of freedom. Unlike traditional 3-axis machines that operate on X, Y, and Z planes, multi-axis machines add rotational axes (A, B, C), providing enhanced flexibility. This allows manufacturers to produce intricate geometries and precise components in a single setup, reducing time, labor, and material waste.
In this article, we’ll explore how multi-axis machining works, its configurations, components, and the numerous advantages it offers. From safety considerations to practical applications across industries, we’ll provide you with a complete guide.
What is Multi-axis Machining?
If you’re looking to bring precision, speed, and complexity to your manufacturing operations, multi-axis machining is your answer. It’s a machining process where tools or workpieces move simultaneously along four or more directions, referred to as degrees of freedom. Unlike traditional 3-axis machines that operate only along the X, Y, and Z axes, multi-axis machines add rotational axes like A, B, and C, giving you greater flexibility and the ability to create intricate parts in a single setup.
Whether you’re in aerospace, automotive, or medical device manufacturing, multi-axis machining is the go-to technology for producing complex, high-quality components efficiently and consistently.
How Does Multi-axis Machining Work?
So, how does this innovative technology function? Multi-axis machining works in several steps to deliver precision and quality:
1. Designing the Part: You start with a detailed design that includes all dimensions and features.
2. Creating a CAD Model: The design is transformed into a 3D model using Computer-Aided Design (CAD) software.
3. Converting CAD to CAM: The CAD file is then converted into a CAM (Computer-Aided Manufacturing) program, which the machine can read.
4. Machine Setup: Operators load the material, configure the machine settings, and transfer the program.
5. Executing the Program: The CNC system automates the tool's movements across multiple axes to complete the part.
6. Finalizing: Operators inspect the finished product for precision and quality.
This step-by-step process ensures that every cut, drill, or milling operation is performed with minimal human intervention, providing a faster and more consistent result than traditional methods.
What are the Main Components of a Multi-axis CNC Machine?
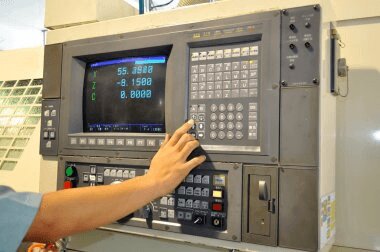
What makes multi-axis machines so advanced? Let’s break it down:
· Machine Frame: Provides stability for precise movements.
· Spindle: Holds and rotates the cutting tool.
· Tool Changer: Automatically switches tools during operations.
· Controller (MCU): The brain of the system that interprets the program and controls movements.
· Driving System: Motors and actuators create precise motion in multiple axes.
· Feedback System: Monitors real-time movements and ensures accuracy.
· Bed and Chuck: Securely hold the material in place.
Each of these components plays a crucial role in ensuring seamless, high-precision machining.
Different Configurations in Multi-axis CNC Machining
To understand the various configurations of multi-axis CNC machining, it is first necessary to understand axes and their types. In CNC machining, an axis represents the direction in which a tool or workpiece moves. Axes can be divided into linear axes (X, Y, Z) and rotary axes (A, B, C). The combination of these axes determines the flexibility and capability of the machine.
Linear Axes and Rotary Axes
· Linear Axes (X, Y, Z):
Represent straight-line movements in horizontal directions (X, Y) and vertical directions (Z). Linear axes define the basic framework for machining operations.
· Rotary Axes (A, B, C):
Represent rotational movements around linear axes:
o A-axis: Rotation around the X-axis.
o B-axis: Rotation around the Y-axis.
o C-axis: Rotation around the Z-axis.
The combination of these axes enables CNC machines to perform complex operations with fewer setups and improved accuracy.
Choose the right multi-axis machine based on your manufacturing needs. Below are some common configurations:
3+2 Axis Machining
Also known as positional 5-axis machining, it combines three linear axes (X, Y, Z) and two rotary axes (A and B) that are used for positioning and locked in place.
· Applications: Suitable for scenarios where real-time 5-axis simultaneous motion is not required. It can machine multiple surfaces of a part and is known for its cost-effectiveness.
4+1 Axis Machining
Includes three linear axes (X, Y, Z) and one rotary axis capable of simultaneous motion (e.g., the A-axis), while the fifth axis is used for positioning.
· Applications: Ideal for parts requiring four simultaneous movements, with the fifth axis locked for machining. Commonly used in mold-making and general machining.
5-axis Machining
True 5-axis simultaneous machining allows three linear axes (X, Y, Z) and two rotary axes (A, B) to move together in real time, enabling dynamic cutting.
· Applications: Suitable for machining complex geometries, such as turbine blades, impellers, and medical implants. It provides unparalleled versatility and precision.
6-axis Machining
Adds a third rotary axis (C-axis) to the 5-axis configuration, allowing 360-degree rotation around the vertical spindle and providing six degrees of freedom.
· Applications: Widely used in automotive manufacturing and large component production, where rapid transitions and efficient cutting are essential.
7-axis Machining
· Definition: Combines three linear axes (X, Y, Z), three rotary axes (A, B, C), and an additional E-axis, which typically provides twisting or articulating motion for the tool arm or spindle.
· Applications: Used for complex part machining that requires extreme flexibility, such as in aerospace and robotics manufacturing. It allows for complete internal and external geometry machining in a single setup.
9-axis Machining
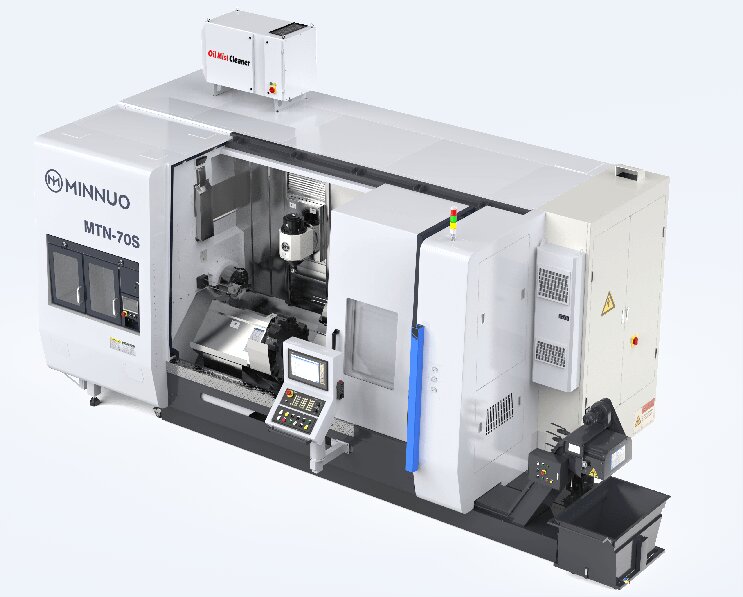
Combines two machining centers, typically a 5-axis mill and a 4-axis lathe, enabling simultaneous milling and turning of the workpiece.
· Applications: Widely used in hybrid machining centers for tasks like machining both the internal and external surfaces of automotive engine parts or complex aerospace components in one setup.
12-axis Machining
Equipped with two 6-axis machining heads, which can operate independently. This allows simultaneous dual machining operations on a single workpiece or two different workpieces.
· Applications: Designed for extremely high-speed production and unmatched precision, commonly found in industries such as medical device manufacturing, watchmaking, and high-performance engine production.
Rotary Table Machining
Incorporates a rotary table that allows the workpiece to rotate around the C-axis, enabling lower-axis configurations to simulate higher-axis capabilities.
· Applications: Suitable for multi-surface machining in 3+2 or 4-axis configurations, particularly in mold-making and prototyping, offering a cost-effective solution.
Tilting Rotary Table Machining
Similar to rotary table machining but with the added ability to tilt the table on a second axis, allowing for more complex angles.
· Applications: Ideal for machining components with intricate angles, such as turbine blades and custom mechanical parts.
Multi-angle Cutting Head
An attachment that allows the cutting tool to tilt at multiple angles during the machining process.
· Applications: Commonly used in aerospace and defense industries for contouring and surface finishing.
What are the Advantages of Multi-axis Machines?
Here’s why multi-axis machining is such a powerful addition to your manufacturing setup:
· Higher Precision: Minimized setups lead to greater accuracy.
· Faster Production: Perform multiple operations in a single pass.
· Enhanced Flexibility: Easily handle complex geometries and material types.
· Cost Efficiency: Fewer setups and less manual labor reduce overall expenses.
· Tool Longevity: Shorter cutting tools reduce vibrations, extending tool life.
These benefits make multi-axis machines indispensable for achieving both efficiency and quality.
What are the Limitations of Multi-axis Machining?
Despite its many advantages, there are some challenges you should consider:
· High Initial Investment: Multi-axis machines require significant upfront costs.
· Complex Programming: Skilled programmers and advanced software are necessary.
· Maintenance Needs: With more moving parts, these machines demand regular maintenance.
· Operator Training: Operating multi-axis machines requires expertise and experience.
Understanding these limitations helps you plan and make the most of your investment.
What are Common Multi-axis Machining Operations?

Multi-axis machines support a variety of operations, such as:
· Milling: For intricate contours and surface machining.
· Turning: Handles cylindrical parts with precision.
· Drilling: Ideal for angled holes and hard-to-reach spots.
· Grinding: Enhances surface finish and precision.
· Waterjet Cutting: Shapes heat-sensitive materials with minimal distortion.
These versatile operations make multi-axis machines suitable for almost every manufacturing challenge.
Applications of Multi-axis Machines in Different Industries
Here’s how multi-axis machines are used across industries:
· Aerospace: Produces turbine blades and engine components.
· Automotive: Creates gears, engine parts, and transmission components.
· Medical: Manufactures implants, prosthetics, and surgical instruments.
· Jewelry and Art: Enables intricate designs and custom creations.
· Marine: Crafts large, durable parts for boats and ships.
No matter your industry, multi-axis machining ensures precision, efficiency, and innovation.
Safety Considerations for Multi-axis Machining
Safety should always come first. Here’s how to ensure a safe operation:
· Use Guards and Barriers: Protect operators from high-speed tools.
· Train Operators: Ensure they know how to handle the machine safely.
· Regular Maintenance: Keep machines in optimal working condition.
· Simulations: Run simulations to prevent collisions or errors during machining.
Following these measures minimizes risks and ensures smooth operations.
How to Choose a Multi-axis Machine?
Picking the right machine can feel overwhelming, but these tips can help:
· Understand Your Needs: Assess whether you need 5-axis or more advanced configurations.
· Consider Cost vs. Value: Don’t compromise quality for lower prices.
· Check Support Services: Reliable after-sales support and spare parts are crucial.
· Plan for Growth: Choose a machine that can scale with your business.
The right choice ensures maximum productivity and a solid return on investment.
Future Trends in Multi-axis Machining
Multi-axis machining is evolving rapidly. Expect to see:
· Micromachining: Essential for electronics and semiconductors.
· AI Integration: Smarter machines with self-optimization capabilities.
· Hybrid Machines: Combining 3D printing and CNC for more flexibility.
· Sustainable Solutions: Energy-efficient machines with minimal waste.
Staying ahead of these trends ensures your business remains competitive.
Endnotes
Multi-axis machining is revolutionizing manufacturing with its precision, efficiency, and versatility. By understanding its capabilities, limitations, and future potential, you can make informed decisions to enhance your operations. Whether you’re crafting intricate medical implants or robust aerospace components, multi-axis machining equips you with the tools to succeed in today’s demanding market.