Gantry Machining: How Much Do You Know?
Over the past few decades, machining technology has undergone tremendous changes. As someone who has been deeply involved in the machine tool industry for many years, I can truly feel the impact these changes have brought. In the past, many complex parts had to be produced through tedious manual operations, which were inefficient and lacked precision. Today, with the application of CNC technology, machining has become efficient and precise, especially with advanced machines like Gantry Machining Centers, which break the limitations of traditional methods and provide higher productivity and quality.
Gantry machining centers, with their high precision, multi-axis motion, and strong rigidity, perform excellently in the machining of large workpieces. Gantry milling machines and Gantry cutting machines offer efficient and precise capabilities in milling and cutting operations.
Let’s take a closer look at Gantry machining.
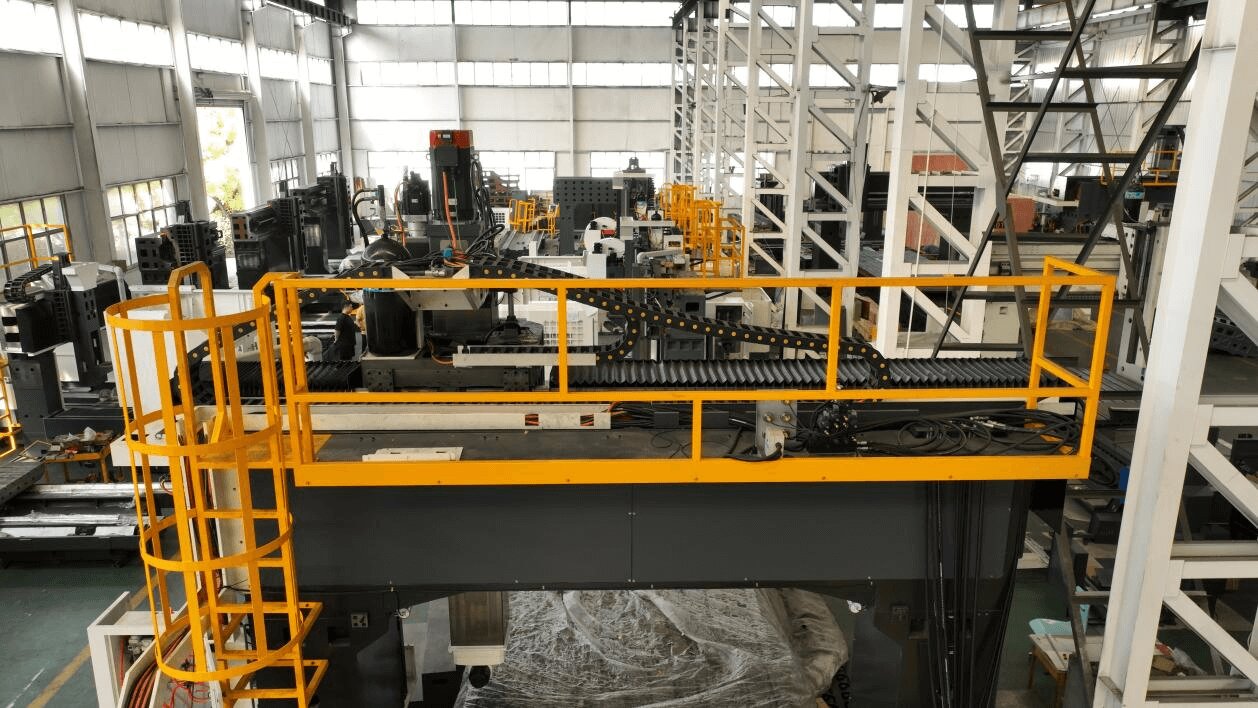
Ⅰ. What is Gantry Machining?
You may have heard of Gantry machining, but do you truly understand how it works and its advantages? Simply put, Gantry machining refers to a CNC machining method that utilizes a gantry-style structure. In this design, the workpiece is fixed on the bed, while the tool head (or spindle) moves along fixed rails, enabling high-precision, multi-directional machining. The common Gantry machining centers usually move in the X, Y, and Z axes, allowing for operations such as milling, drilling, and even complex cutting tasks.
Compared to traditional machining methods, the greatest advantage of Gantry machining is its precision and stability, making it especially suitable for processing large workpieces.
Ⅱ. Gantry Machining Centers
If you're considering purchasing a Gantry machining machine, it's important to have a clear understanding of what a Gantry machining center is. It’s not just a large machine tool; it is a high-precision, high-rigidity, and high-load capacity machining system. Here's why it's so unique:
Key Features:
Multi-Axis Motion: Gantry machining centers usually support movement in the X, Y, Z, and sometimes additional axes, adapting to a variety of complex machining needs. This means they can handle more difficult parts, whether they are intricate 3D components or high-precision aerospace parts.
Large Workpiece Capability: The design of the Gantry structure allows the machine to span a large area, making it capable of processing oversized workpieces. If your industry requires large workpiece processing, Gantry machining is undoubtedly your best choice.
Rigidity and Stability: The Gantry structure itself offers excellent rigidity, allowing the machine to withstand large cutting forces during machining, reducing vibration and ensuring high precision in the final workpiece.
Why Choose It?
For many manufacturing businesses, purchasing a Gantry machining center is more of a technological investment than just acquiring a piece of equipment. If you have high-precision, high-volume machining needs, a Gantry machining center will undoubtedly help improve production efficiency and product quality. By reducing machining errors and increasing processing speed, you can lower costs and enhance market competitiveness.
Ⅲ. Gantry Milling Machines
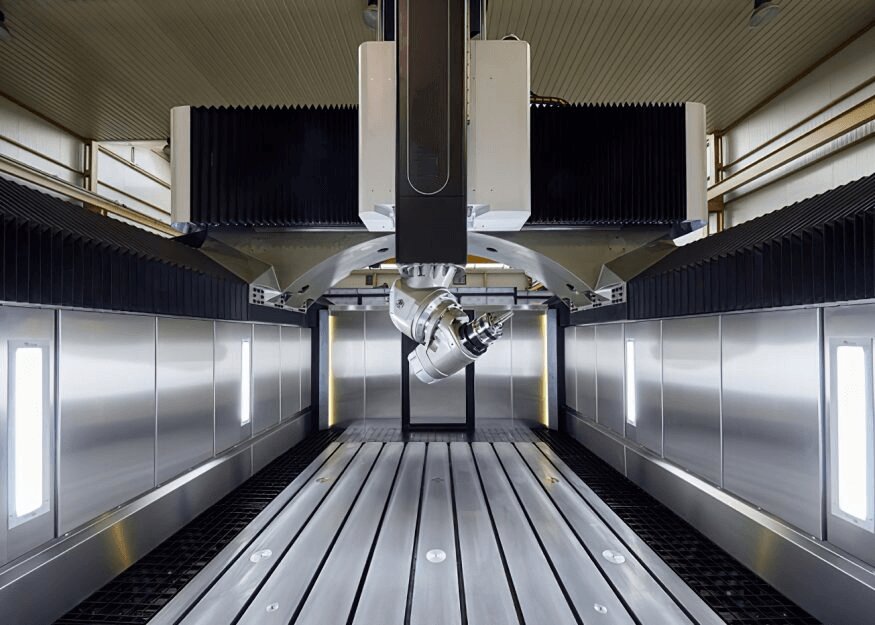
Among the various Gantry machining machines, Gantry milling machines are one of the most common types. As a high-precision, high-efficiency milling tool, a Gantry milling machine can meet a wide range of complex milling tasks, especially in cases requiring large-area machining or high-precision requirements.
Key Features:
Precise Milling: Whether it’s milling large aluminum alloy parts or machining complex curved surfaces of metal components, the Gantry milling machine can provide stable machining precision.
Strong Load Capacity: Compared to other milling machines, Gantry milling machines have stronger load capacity, making them suitable for handling heavier workpieces and tasks that require high cutting forces.
High Flexibility: The machining methods of Gantry milling machines are highly versatile and can be customized according to different needs, fulfilling the personalized machining requirements of customers.
You may wonder if such a high-precision machine would be expensive. In fact, in the long run, a Gantry milling machine can significantly increase production efficiency and reduce manual intervention, making it a worthwhile investment for any company looking to enhance its productivity.
Ⅳ. Gantry Cutting Machines
In addition to milling, Gantry machining machines also perform brilliantly in cutting. Gantry cutting machines, utilizing the Gantry-style structure, employ high-precision cutting tools such as laser cutting, plasma cutting, or water jet cutting to efficiently and precisely cut large workpieces.
Advantages:
Precise Cutting: Whether it’s metal, plastic, or ceramics, Gantry cutting machines can provide extremely fine cutting precision, making them especially suitable for industries with high cutting quality demands.
High-Volume Production: If you require large-scale production, Gantry cutting machines offer higher cutting speeds and efficiency than traditional cutting machines.
Variety: The diversity of cutting technologies (such as laser, water jet, etc.) enables Gantry cutting machines to select the most suitable cutting method for different materials, meeting various manufacturing needs.
Ⅴ. How to Avoid Errors in Machining
As an operator, avoiding machining errors is key to ensuring high-precision results. When dealing with complex Gantry machining tasks, errors not only affect the quality of the workpieces but could also lead to equipment damage. So, how can we avoid these problems?
Improving Machining Accuracy:
1. Regular Calibration: Perform precise calibration before starting the machine every time to avoid minor errors.
2. Monitor Tool Wear: Replace worn-out tools in time to prevent tool performance degradation from affecting machining quality.
3. Accurate Programming: Avoid programming errors by using simulation software to check the program in advance, ensuring each step is accurate.
4. Prevent Thermal Expansion: During machining, control the temperature of both the machine and workpiece to prevent errors caused by thermal expansion.
By now, you should have a clearer understanding of Gantry machining. It’s not just an investment in machinery, but also an investment in improving your overall productivity. If you’re ready, start choosing the right Gantry machining center for your needs.
Ⅵ. MINNUO: Reliable Manufacturers You Can Choose
MINNUO’s Gantry machining machines are all certified with ISO, CE, and other international standards, ensuring that each piece of equipment meets global manufacturing standards. These certifications not only guarantee product quality but also reflect our international level of technology, management, and manufacturing processes.
We also support personalized customization. MINNUO’s strong and responsive pre-sales department can provide machine recommendations within 10 minutes for a single piece of equipment, and for production lines involving multiple machines, we can provide solutions within 5 working days.
Our services go beyond a one-time support after product delivery; we provide full lifecycle support, including purchase, installation, commissioning, and daily maintenance. Our 24-hour technical support service ensures quick problem resolution, whether through remote video, phone, or on-site services.
Conclusion
If you’d like to know more about Gantry machining or need more detailed information about our products, feel free to contact us, and we’ll provide you with professional answers!