Key Consideration For Choosing The Right Cnc Machine Tools
As global manufacturing continues to evolve, the importance of CNC (Computer Numerical Control) machine tools has become increasingly evident. From Germany’s reliance on precision CNC machines in high-end manufacturing to the growing demand from emerging economies like India and Vietnam, CNC machines are indispensable across various industries.
The market for CNC machine tools is vast and varied, with numerous brands and models ranging from basic entry-level CNC milling machines to high-end multi-axis machining centers, resulting in significant differences in price and performance. To accurately select equipment that fits your needs, factors such as cost, manufacturing quality, spare parts availability, warranty, safety features, and machine components must be considered.
Let’s dive into the key factors to consider when choosing the right CNC machine tool.
Ⅰ. Begin with cost
When purchasing a CNC machine tool, cost must be assessed comprehensively, covering the following aspects:
· Initial Purchase Price: CNC machines vary widely in price. For instance, a basic entry-level CNC milling machine may cost around $10,000, while a high-end multi-axis machining center equipped with high-speed spindles, automatic tool changers, and precision cooling systems can exceed $500,000.
· Software Costs: Operating CNC machines requires software. Certain machines need specialized CAD/CAM software, which can significantly increase overall costs due to licensing fees.
· Training Costs: Training employees to operate machines is essential. Costs can range from a few hundred to several thousand dollars, depending on machine complexity and training providers.
· Consumable Costs: Don’t overlook the costs of consumables such as cutting tools, coolants, and lubricants. In high-volume production environments, these costs accumulate over time. For example, a busy manufacturing plant operating multiple CNC machines may spend thousands of dollars annually on cutting tools alone.
Ⅱ. Manufacturing Quality
The Core Role of Manufacturing Process Quality
In precision manufacturing, the quality of the CNC machine’s manufacturing process is paramount. It directly affects dynamic performance, long-term machining accuracy, and overall reliability throughout the machine’s lifecycle. High-quality CNC machines employ advanced techniques, like finite element analysis (FEA), during the design phase to ensure components maintain optimal mechanical properties and motion precision under complex conditions. Strict adherence to quality management systems (such as ISO standards) ensures full-process quality control—from raw material procurement and component machining to final assembly and testing.
Impact of Manufacturing Materials on Machine Performance
The choice of materials significantly influences the machine’s overall performance. Typically, the machine’s main frame and key moving components (e.g., bed, column, worktable, spindle) are made from high-rigidity, high-damping alloys such as quality cast iron or high-strength alloy steel. These materials excel in mechanical properties, effectively minimizing vibrations and deformations during high-speed cutting or heavy-load machining. For example, a machine bed made from ductile cast iron, with its spherical graphite distribution, provides excellent vibration absorption and high compressive strength, laying a solid foundation for high-precision machining.
Ⅲ. Critical Impact of Machine Components on CNC Machine Selection
Achieving high-precision machining is a core goal, and the accuracy of key machine components is essential.
Spindle Assembly
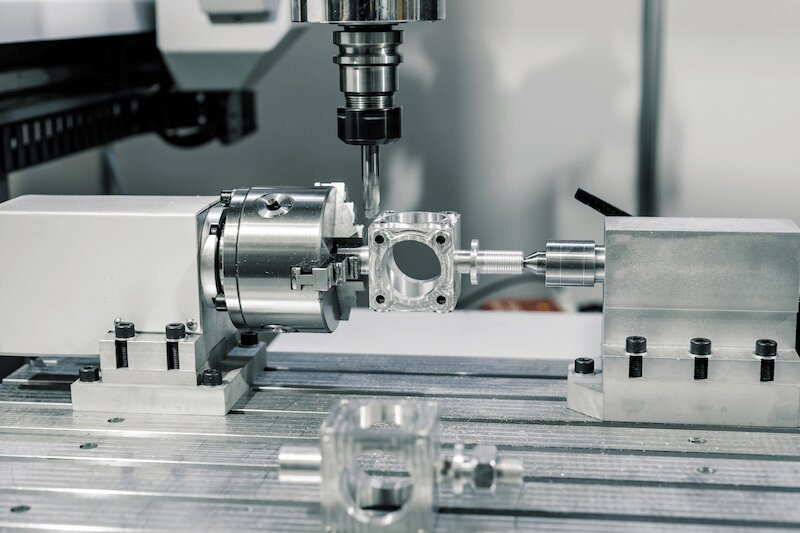
· Spindle: The core component, with its rotational accuracy, determines machining precision. Key factors include radial runout, axial play, and errors caused by spindle imbalance. In milling, excessive radial runout can cause waviness on the machined surface, while abnormal axial play leads to unstable milling depth and significant part size deviations. Additionally, errors caused by spindle imbalance can also reduce machining precision, affecting surface flatness and dimensional consistency. For applications such as aerospace engine blade milling, high-precision spindles are crucial for ensuring accuracy, requiring strict control over precision parameters.
· Spindle Bearings: These affect the spindle’s rotational stability. Evaluate bearing types and precision grades. High-precision angular contact ball bearings or tapered roller bearings minimize spindle runout. Worn bearings or poor lubrication can increase spindle motion errors, reducing machining accuracy. For example, high-speed grinding wheels in precision grinders rely on top-grade spindle bearings.
Guideway Components
· Machineay Bed Guidews: These determine the movement accuracy of components like the worktable. Key indicators include straightness, flatness, and surface roughness. For large mold machining on gantry milling machines, guideway straightness errors can cause inclined or wavy milling surfaces, affecting overall precision.
· Sliding Blocks: Working with guideways, sliding blocks affect movement stability and accuracy. Consider material quality, manufacturing precision, and fit accuracy. Worn sliding blocks cause component wobbling or sticking, compromising cutting accuracy. On CNC lathes, sliding block accuracy impacts tool positioning and part surface quality.
Ball Screw and Nut Assembly
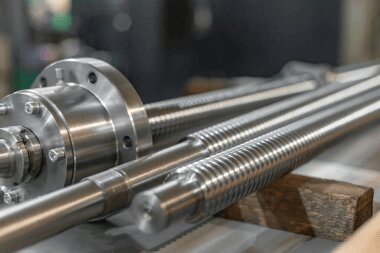
· Ball Screw: This determines positioning and feed accuracy. Key indicators include lead accuracy, straightness, and surface quality. Insufficient accuracy in complex contour machining (e.g., CNC machining centers) leads to deviations between the programmed tool path and actual part contours. High-precision ball screws are vital for intricate applications like optical lens mold machining.
· Nut Assembly: Clearance between the screw and nut affects transmission accuracy and efficiency. Large clearances cause table crawling and severe accuracy loss; overly tight fits increase friction, affecting ball screw lifespan.
Tool Change System Design
· Magazine-Type Tool Changers: Accommodate 10 to over 100 tools, suitable for complex operations requiring frequent tool changes.
· Turret-Type Tool Changers: Simpler and ideal for smaller machines with less complex tasks, offering relatively faster tool changes.
For more information on tool changing devices, you can read: What is an Automatic Tool Changer and the 4 Common Types?
· Tool Change Speed: High-speed changers complete swaps in seconds, significantly boosting efficiency in mass production settings.
Ⅳ. Spare Parts Supply & Warranty
Spare parts availability is crucial to minimize downtime. Research the manufacturer’s spare parts network. Brands with extensive global distribution networks ensure quick parts availability, whereas sourcing components for niche models may pose challenges, extending lead times and potentially halting production lines.
A comprehensive warranty reflects the manufacturer’s confidence in their product. It should cover manufacturing defects and offer replacement and repair support within the warranty period. A longer warranty (e.g., three to five years) provides peace of mind and protects your investment.
Ⅴ. Safety – A Critical Aspect of CNC Machine Tools
Safety is non-negotiable with CNC machines, given their high-speed operations and significant forces. Choose machines with adequate safety guards to prevent operator contact with moving parts. Emergency stop buttons should be easily accessible and clearly marked.
Modern CNC machines often include advanced safety features like collision detection systems, which immediately halt operations if abnormal movement or potential collisions are detected, preventing damage to the machine, tooling, and workpieces. Proper grounding and electrical safety measures are also essential to protect operators from electrical hazards.
VI. Significant Advantages of MINNUO CNC Machine Tools
(1) Advantages of Machine Tool Components
Spindle Components:
MINNUO CNC machine tools utilize a thermally symmetric structure design for the spindle, paired with a constant temperature cooling system that effectively suppresses thermal deformation. The radial runout accuracy is controlled within 0.001mm, and the axial movement accuracy is maintained within 0.002mm. The bearings are high-precision P4-grade angular contact ball bearings. The internal clearance of these bearings is specially pre-adjusted to maintain very low vibration and noise levels during high-speed operation, significantly enhancing the stability of spindle rotational accuracy, ensuring high-precision machining over extended periods.
Guide Rail Components:
The slider and guide rails use a unique dovetail slot matching structure, with the contact surfaces specially heat-treated, achieving a hardness of HRC58-62. This treatment improves wear resistance by over 50%. Additionally, high-viscosity guideway oil imported from Germany is injected to ensure smooth operation of the moving parts under high speed and heavy load. The positioning accuracy can reach ±0.005mm.
Ball Screw and Nut Assembly Components:
The ball screws are made from high-quality alloy steel imported from Japan, processed using high-precision grinding techniques. The pitch accuracy is up to ±0.002mm/m, and the straightness error is less than 0.003mm per meter. The nut and ball screw pairing adopts a ball circulation structure, with the consistency error of the ball diameter controlled within 0.0005mm. The fit clearance is controlled between 0.001mm and 0.003mm.
Tool Change Mechanism Design:
The tool magazine-style tool changer can accommodate a wide variety of tools, with a capacity of up to 120 tools. The tool change speed is as fast as 2-3 seconds. The turret-style tool changer has an optimized design, leading the industry in tool change speed compared to similar equipment.
(2) Spare Parts Supply and Warranty Advantages
MINNUO has a global spare parts supply network, with spare parts centers located across all major continents. The company works with numerous authorized dealers and offers a 24-hour response time, with spare parts delivered within 48 hours. MINNUO provides an extended five-year warranty service, covering manufacturing defects as well as parts replacement and repair services within the warranty period.
(3) Safety Advantages
The machine tools are equipped with comprehensive safety protection devices, including protective doors and light curtain sensors. The emergency stop button is large and clearly marked. An advanced collision detection system has been integrated, using high-precision sensors and intelligent algorithms to provide instant response. Regarding electrical safety, MINNUO strictly adheres to international standards, employing multi-grounding and leakage protection measures.
Ⅶ. Conclusion
Selecting the right CNC machine tool is a complex decision that demands a thorough evaluation of multiple factors. By considering costs, manufacturing quality, spare parts availability, warranty coverage, safety features, tool change system design, power capacity, and key components, you can make an informed choice that aligns with your manufacturing needs and objectives.
Understanding these factors can significantly shape your manufacturing efficiency and competitiveness for years to come. If you still have questions about selecting the right machine tool, feel free to visit MINNUO—we offer professional, free consultations to help you make the best choice!