Climb Milling or Conventional Milling: Which One Should You Use?
In CNC machining, the choice of milling method may seem subtle, yet it can have a significant impact on machining accuracy, tool life, surface quality, and even the overall stability of the machine. The decision between Climb Milling and Conventional Milling is not merely a theoretical debate, but a critical process selection point that engineers must thoroughly understand and apply correctly.
Climb milling refers to the situation where the direction of the cutter rotation is the same as the feed direction, with the cutting edge engaging the material at its thickest point. In contrast, conventional milling means the cutter rotates against the feed direction, starting the cut at the thinnest section.There is no absolute answer as to which method is better—only a rational decision based on which is more suitable under specific conditions.
This article will take an engineering-oriented approach to systematically analyze the mechanical differences and influencing factors of the two milling methods, and provide clear and practical selection criteria.
1. Climb Milling:
Climb milling refers to a cutting method in which the cutter rotates in the same direction as the feed of the workpiece. The cutting edge engages the material at its thickest point and gradually cuts thinner. It is one of the most common milling methods in modern CNC precision machining.
Technical Essentials:
•The cutting force pushes the workpiece against the fixture, theoretically reducing vibration and backlash;
•The tool bears the highest load at the entry point, making it more prone to instantaneous impact;
•Chips are expelled away from the machined surface, minimizing secondary cutting and surface damage.
Advantages:
•Lower surface roughness, suitable for finishing and final contour milling;
•Slower tool wear and lower cutting temperature;
•Smoother chip evacuation, which aids cooling and chip removal
⚠️ Risks & Limitations:
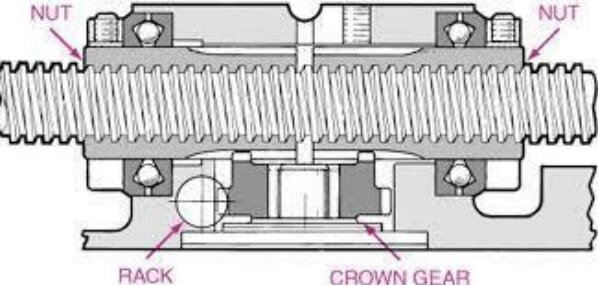
•The cutting force can pull the table in the reverse direction, requiring precise backlash compensation of the machine leadscrew;
•If the fixturing is insufficient, the impact may pull the workpiece or tool;
•In thin-walled parts or low-rigidity materials, climb milling may lead to increased vibration.
✅ At MINNUO, we often apply climb milling in the precision machining of lightweight materials such as aluminum, copper, and plastics. Especially on 3-axis and 5-axis CNC machines, paired with high-rigidity toolpath planning, this method helps us achieve excellent balance between efficiency and surface quality.
2. Conventional Milling:
Conventional milling is where the cutter rotates opposite to the feed direction of the workpiece, starting from the thinnest part of the material and cutting deeper. This method is more suitable for traditional vertical and horizontal milling machines, as well as older CNC machines with significant backlash.
Technical Essentials:
•The cutting force lifts the workpiece, generating a reactive force;
•The initial cutting thickness is low, helping reduce entry impact — ideal for older equipment or harder materials;
•Chips flow in front of the cutter, which may cause secondary friction.
Advantages:
•Gradual cutting load on tool entry, suitable for roughing or interrupted cuts;
•High tolerance to machine backlash, less likely to cause table creep;
•Even when clamping is insufficient, the risk of workpiece displacement is relatively low.
⚠️ Limitations:
•Poorer surface finish that often requires secondary finishing;
•Faster tool wear, especially in hard material machining;
•Chip accumulation increases cutting heat, and poor cooling may cause built-up edge (BUE).
3. Climb vs Conventional Milling: Not Just Direction, But a Matter of Cutting Dynamics and System Matching
Comparison Aspect | Climb Milling | Conventional Milling |
Cutting Force Direction | Downward → Improves stability | Upward → Increases risk of displacement |
Tool Load at Entry | Heavy → High impact | Light → Smoother engagement |
Tool Wear & Life | Less wear → Better cost control | Faster wear → Better for roughing |
Surface Finish | Better → Suitable for finishing | Poorer → Requires post-processing |
Sensitivity to Backlash | High → Requires rigid CNC machines | Low → Tolerant to old/manual machines |
Cooling and Chip Removal | Chips move away from surface → Good heat dissipation | Chips accumulate ahead → Requires effective cooling |
4. How to Make the Right Choice? These Four Key Factors Must Be Considered
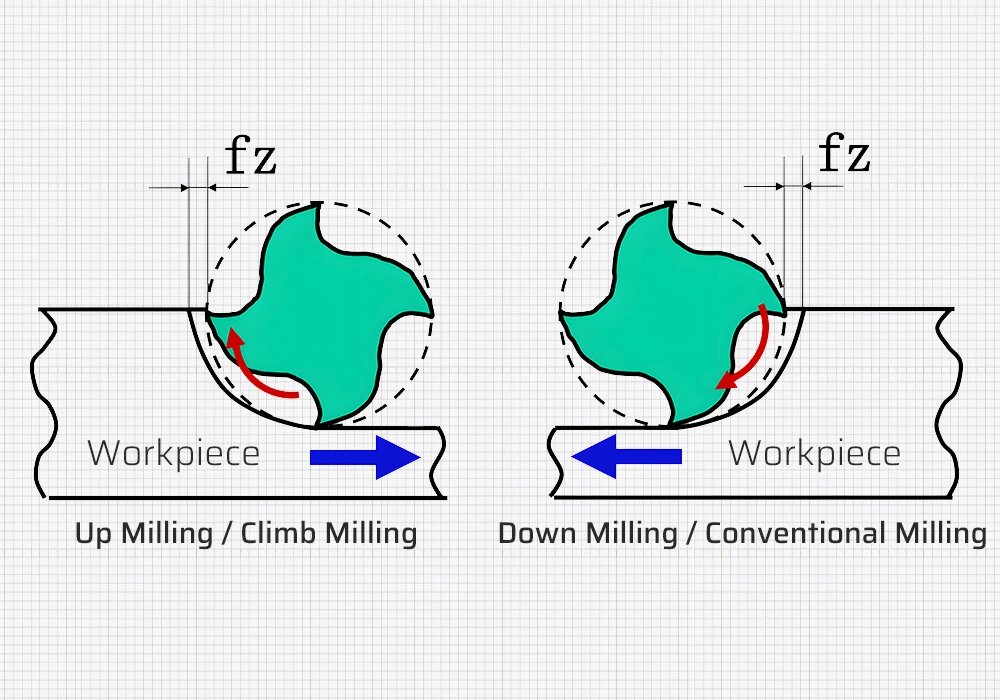
The choice between climb milling and conventional milling is not simply about machine age, but should be based on the overall process system. The following four variables are critical in making the correct decision:
① Workpiece Fixturing and Support Rigidity
•Firm clamping and solid base → Climb milling recommended
•Weak fixture or low positioning accuracy → Conventional milling is safer
② Material Characteristics
•Soft metals (aluminum, copper, plastic) → Prefer climb milling
•Hard/brittle materials (hardened steel, cast iron) → Consider conventional milling to reduce tool chipping
③ Tool Selection and Cooling Conditions
•High-rigidity tools + effective cooling → Climb milling performs better
•Regular alloy tools + limited cooling → Conventional milling is more stable
④ Machining Objective
•For high surface quality and accuracy → Climb milling preferred
•For high material removal rate and roughing → Conventional milling more suitable
5. Conclusion: The Right Milling Method Is the Result of System Matching
Climb milling is not inherently superior, and conventional milling is not outdated. Each serves different goals based on the machining environment, material, and tool setup. The choice of milling strategy is essentially about system-level coordination among machine, fixture, tooling, and process objectives.
At MINNUO, we do not rely on default habits to choose milling direction. Instead, we base every decision on process evaluation, fixture analysis, and toolpath simulation, ensuring that every project is assigned the most appropriate milling strategy — delivering the optimal balance of efficiency, quality, and cost.
Choosing the right process is the first step toward successful manufacturing.